9 Continuous Improvement Methodologies & Tools
Not all change leads to improvement, but to improve anything, you need to bring about change. Usually, that’s easier said than done. Greatly enduring organizations have survived over the years through continuous improvement and incremental innovations.
What does it take to bring about improvements in a systematic and structured way? Besides the right mindset, culture, and capabilities, you need methodologies and tools to fuel and maintain these improvements.
While sometimes disregarded, methodologies provide a solid starting point for continuous improvement. Without a set of shared practices to guide the path, organizations tend to play it by ear, and that’s not something you want for long term success. What’s more, to implement and operate such methodologies, you need the right tools and techniques.
If you want to learn more about some of the best tools out there, what to consider when choosing the right ones, and how to implement them to unlock their full potential, keep on reading. We’ll walk you through a list of tools and best practices that will help you take continuous improvement practices to the next level.
Table of contents
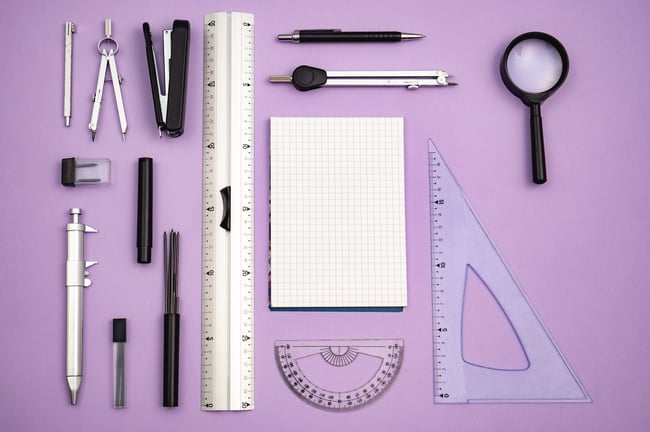
The role of methodologies and tools in continuous improvement
Apple is a leading example when it comes to innovation, but let’s not forget that its success is mostly due to incremental innovations. The smartphone already existed when the iPhone entered the market, but Apple turned it into a mainstream success through significant improvements on the size of the touchscreen, an enhanced overall experience, the app store and later their own ecosystem that became the center of our daily lives.
To this day, Apple has maintained its positions through small changes and improvements, but they are not the kind that have a profound impact on our lives. On the other hand, the internet and its commercialization were innovations that allowed many new industries and businesses to emerge, and it completely changed our society. Such innovations are far less common than incremental ones, and a lot more difficult to achieve.
That’s not to say that incremental innovations are a breeze. There are so many things to improve whether you are developing products or services. The true challenge lies in how to approach continuous improvement in a sustained manner. How do you manage improvements systematically to turn them into a common practice? There are three key elements to consider:
-
Start with a goal that matters the most for your business strategy
You need to know what you’re aiming for and not change things for the sake of change. The purpose of continuous improvement should be to make certain areas that are relevant for the strategic goals of the organization better. -
Decide on the methods and processes that can support that goal
The methods and processes provide guidance and a roadmap to help you reach the desired results. If you have these in place it’s easier to stay focused on the goal. -
Choose the tools that bring to life the methods and processes.
There’s a wide variety of tools and techniques that can be used in continuous improvement. Deciding on one, or several comes down to your current state and obviously, future goals.
For instance, Toyota, the pioneers of organizational continuous improvement, developed their own methodologies and tools that enabled them to become market leaders. However, this took many years of preseverance which led to a new mindset and culture.
Methodologies and tools for implementing continuous improvement
Instinctively, people check the competition to replicate their methods or the use of their tools. Even though it’s not wrong to get inspired, benchmarking what others are doing is not enough to set up your own continuous improvement system.
To make things easier, we listed below some of these methodologies and the tools that work for each of them, as well as some tips and best practices for implementation.
1. Kaizen corner
As the most common concept in continuous improvement is Kaizen, it’s only natural to start the list with the Kaizen Corner. We previously talked about continuous improvement processes, so you can explore the Kaizen concept more in depth here.
What is it: So, the Kaizen corner obviously draws its name from the Kaizen concept, the Japanese management methodology loosely translated as continuous improvement, or literally, good change (kai = change, zen = good). Hence, the Kaizen corner is a place where employees can submit ideas and improvement suggestions. While originally used in factories and areas where employees were not in direct contact with top management, today it’s applied in a variety of industries, including software.
This bottom-up approach is meant to involve everyone in the organization in the continuous improvement practices. A Kaizen corner is a great tool to spot new opportunities for improvement, engage with employees and on the long run, contribute to a continuous improvement culture.
It's well suited for teams working in logistics, or other industries where they don’t have easy, regular access to digital tools. These are the employees whose feedback is most often neglected, but whose tacit knowledge can bring up unexpected opportunities. Just as well, you can use this in a digital format with an idea management tool, or a project management tool. It brings even more value because it provides more structure and transparency to the process.
Tips for implementation: Listening to your employees’ ideas, concerns and suggestions is always beneficial, but it shouldn’t stop there. For long term success, you need to act on those ideas, communicate, and follow-up on them.
Recommended tools: If you start small, with a team that works in the same space, where digital tools are not at hand, like construction sites, hospitals, factory floors, then the old-school tools are always a good option. These could be as simple as post-it notes on a wall or a suggestion box.
On the other hand, if your teams have access to digital tools or you want to bring together remote teams, an idea management tool like Viima is the solution. You can use it to collect ideas from hundreds and even thousands of employees.
Another digital option used for project management and writing down ideas is Trello, a tool built on the principles of the Kanban system, which we'll cover next.
2. Kanban
What is it: Kanban means "visual sign" in Japanese and it’s used in many organizations, whether they use the official name or not. As a concept, Kanban is a lean method used to manage and improve work across systems. It’s generally applied through Kanban boards, cards or flows that describe the roadmap of a project and the status of each element. It's an easy method of improving efficiency.
Kanban boards are commonly used in product management and development, so basically every organization could make use of this methodology. It’s easy to implement, it improves processes and workflow efficiency without making any changes to your team structure.
Tips for implementation: The steps for implementing Kanban are quite straightforward, but the important thing is to monitor the roadmap and adjust it as needed. As the project progresses, every stage of the process has its milestone and sometimes bottlenecks might come in the way. If this is the case, you can go to the root cause analysis, which we’ll cover next, to identify the cause of the bottlenecks, then work to eliminate them or prevent them from stopping or slowing down the process.
Recommended tools: Trello and Jira are some of the most popular tools for Kanban practices, but there are many others you can choose from. Something as simple as an Excel or Google sheet can be used to organize the steps and milestones. For larger projects and teams, though, it might become messy.
Viima is not just a tool to collect ideas, but it scales with your needs and allows you to organize, monitor and develop different boards and flows. What's more, Viima comes with a Jira integration, which allows you to connect preferred Viima statuses with kanban stages in Jira and allows for new Jira issues to be created automatically when the idea in Viima moves to the first connected status phase.
Root cause analysis
Many organizations don’t excel at continuous improvement because they either don’t know how to prioritize the things that need improvement, or they haven’t identified the real causes behind certain issues.
So, here are two methods that can help you with this.
3. 5 whys
What is it: A popular tool used to get down to the root cause of issues. With the 5 Whys you can explore more in depth the factors that influence an outcome and go from contributing factors to root causes that lead to a problem.
For example, if a team was late in delivering a product, you want to learn why that happened and what could have been done differently. Likewise, you might see that productivity has decreased. Maybe more people are taking a sick leave than before, so you can assume that is the reason. But if you dig deeper, can you find out why are sick leaves more recurrent than before? The 5 Whys can also help reframe the thinking and eliminate biases.
Tips for implementation: While you could apply this in your own thinking, for more complex problems, it’s best to gather a knowledgeable team who can help you in the process. For this, you can create a time-bound session around a specific problem that needs a solution. You define the problem beforehand and bring people together and start exploring all sides of the issue with the 5 Whys exercise. For a better workflow you can have a facilitator to guide the session and write down ideas.
Recommended tools: The 5 whys doesn’t need any special tool, but to document the process better we added some templates to our Continuous Improvement Toolkit. However, keep in mind that the 5 whys is not a methodology to be used on its own. It’s part of a process that helps you get down to the root cause of an issue and then work on improvements to address that.
In your continuous improvement work, you will probably have to use the 5whys technique more than once for the same area or project. For this, you can use a flexible idea management tool. For example, you can simply add to a Viima board these questions where people will provide answers and suggestions. In time you will start noticing connecting ideas, trends, patterns, and recurring issues that will help uncover more opportunities for improvement.
4. Fishbone diagram
What is it: Also called the Ishikawa diagram, this is a diagram used as a root cause analysis, to show potential causes of an event. It was first described in the 60s by Professor Kaoru Ishikawa as a quality control tool. The fishbone diagram is mostly used in product design and quality defect prevention to identify the factors that could cause an effect.
For example, the CMS (Centers for Medicine & Medical Services) is showing how they’re using the fishbone diagram in their quality assurance and performance improvement (QAPI). In this case they dig deeper to learn what systems and processes lead to a patient’s injury while under medical care.
The drawback of the fishbone diagram is that for more complex issues the interrelationship between causes can complicate things. What’s more, it’s not always easy to point to all the factors that make a problem. At the same time, there might be so many elements to point at, that it’s messy to handle them in a simple diagram model. So, it takes some experience and a knowledgeable team to work with the tool, as well as the right context for it.
Tips for implementation: If unsure about how to get started, some people first use the 5 Whys method to create the main structure and identify each cause-and-effect element that will be developed in the fishbone diagram.
Recommended tools: The fishbone diagram doesn’t require a specific tool for implementation. You can use a template like the one available in our Continuous Improvement Toolkit or make your own on from scratch on a whiteboard, during a brainstorming session. There are also countless tools out there for flowcharts and diagrams. Some of these are Visio from Microsoft, Lucidchart or Smartdraw.
5. Gemba walks
What is it: The Gemba walk is another popular tool in the continuous improvement toolkit. Simplified, it’s an observation practice where managers and leaders stay in touch with the ins and outs of the organization. “The place to be”, the meaning of Gemba in Japanese, refers to the areas where value is created in an organization. So, understandably the Gemba walks are meant to be applied in areas where things get done. This can be the shop floor in manufacturing, operating room in a hospital, construction sites, and so on.
Even though it doesn’t sound like much, in reality a Gemba walk is not a walk in the park. It requires experienced leaders who can spot things from the distance as well as careful planning.
Tips for implementation: As mentioned, Gemba walks should have a well-defined plan and a clear purpose. First, think of what you want to achieve with the Gemba walk. Is there something specific that you want to learn, understand, improve or address? Do you want to check the state of processes that are used, or how the lines of communication work.
Another thing to keep in mind is that during these Gemba walks leaders should not interrupt or point to things others should fix. Your role as a manager or leader performing a Gemba walk should be to observe and be open to understanding what others are doing and why.
A roadmap of areas you want to cover can come in handy here (for example you start with sales, and continue down the line to shipping, assembly line and so on). Prepare a checklist, especially at first, when you are still getting the hang of it. Below you can see an example of a Gemba walk plan at Toyota.
Recommended tools: While the easy way out is to look for examples of how others are doing it, it’s better to customize a checklist and a list of questions based on your strategic goals and organizational needs.
We created a Continuous Improvement Toolkit where you can find a set of useful tools, as well as a checklist with questions to address when planning your Gemba walk. You can download it for free, here.
6. Value stream mapping
What is it: Value stream mapping is a visual tool used to illustrate and structure the steps involved in the process of delivering a product or service from supplier to customer. The visual representation of such processes helps analyze, manage, and identify inefficiencies and opportunities for improvements within the value stream.
As is the case with other tools and methods in Lean methodology, VSM was initially used in manufacturing, but it has been adopted in many other industries due to its effectiveness in continuously improving productivity and reducing and eliminating waste. A value stream map is meant to showcase the processes and relationships in manufacturing, production, scheduling and so on.
For example, in software development the value map streaming can be used to identify inefficiencies in the development process. Consequently, the team can reduce the number of steps or redundancies.
Tips for implementation: First and foremost, start with a problem that needs to be fixed. Based on this, you collect data, make different analyses, and look for solutions. To have a better overview and to be able to identify the weak spots and inconsistencies, you draw the current state map. This way, you’ll get a better understanding of the flow of information and materials. Now you can make a list of possible improvements for each issue you identify. Last, you create the future state map to draw the desired state of the process, after improvements.
This is a useful tool for organizations that work with complex processes that have multiple touch points. However, it’s not a multi-purpose tool that can be used for all kind of problems. The main purpose is to reduce waste, so if you have an issue that is not connected to the flow or you don’t have a linear flow of information and material, this might not do the trick for you.
Recommended tools: Each value stream map looks different for every organization, but the core steps to follow are similar for most. There are various diagramming tools that you can use to create a value stream map. Lucidchart from Lucid is a viable solution to create diagrams, as well as Visio from the Microsoft Office family.
In our Continuous Improvement Toolkit you can find more information about the steps to follow when creating your value stream mapping.
7. 5s
What is it: The 5s is a tool used to create a clean and orderly work environment that exposes waste and abnormalities. It can be used to identify improvements in the workplace through the following five actions:
- Sort (Seiri) is about arranging all items and eliminating unnecessary things from the workplace.
- Set in order (Seiton) is about putting everything in order, to its designated space, so they are easy to locate.
- Shine (Seiso) is about a clean workspace that creates a safe, easy to work environment.
- Standardize (seiketsu) helps you establish procedures and schedules that ensure the repetition of the previous three practices.
- Self-discipline (sustain). Last, but not least, in order to turn these into a continuous practice, you have to ensure that the approach is followed and that it becomes a habit for employees.
As the terms reveal, the 5S framework is designed first and foremost for physical workplaces, such as factory floors. However, these same principles are just as valid in the modern workplace, a hybrid between physical and virtual. The 5S has now been adopted in different industries like healthcare, education, and government.
The 5S has become a building block for most lean tools and concepts today. The benefit is that it’s low cost and high impact as it doesn’t require a lot of money to implement it.
Tip for implementation: To successfully implement 5S practices, it’s mandatory to have top management support. Leaders should set the example, provide training at all levels and delegate a responsible for each area. Their commitment, together with an action plan will ensure continuity of the 5s practices.
Additionally, audits are important to keep the program alive, monitor its evolution and results. Like most continuous improvement tools and methodologies, this one too, comes with its set of challenges. There might be resistance from some people, and lack of alignment on how the concepts should be applied.
Also, it can become challenging to provide continuity if key players in the program leave the company or if there are changes in the team structures. To prevent this from happening make sure that everything is well documented, for example in an implementation manual that explains the principles, structures, and activities.
Recommended tools: The tools you choose will greatly depend on the environment of your organization and each S in part. While there might be different tools for each S, to avoid getting lost in all the options, it’s best to draw a plan and create an audit checklist, as well as keep track of the results of the audits.
For this, you can even use a Google form to create an audit checklist that suits your environment. But to help you out, the Continuous Improvement Toolkit also comes with an audit template.
8. Error Proofing
What is it: The error proofing (or mistake-proofing from the Japanese Poka-Yoke) is another methodology applied in lean management and manufacturing. Error proofing is generally used as a standardization technique to ensure that all conditions are met to perform the steps of a process.
The error proofing can be implemented wherever there are processes that depend on people’s skills, experience, and attention. To name just a few, think of the de-icing layer applied on the planes’ wings before each take-off to prevent serious accidents, the color coding on wires to prevent short-circuiting, or the electric sockets designed to prevent wrong plugging.
The cost of not preventing errors and mistakes can be huge for companies. Dell and Sony lost roughly $400 million when they had to recall over four million laptops whose lithium-lion batteries became a fire threat.
Tips for implementation: For successful implementation of error proofing, you either need to prevent errors from happening or detect them when they occur. Similarly with the other tools and methodologies, commitment and support from top management is essential, as well as an action plan to disseminate the right practices.
Recommended tools: The beauty of the various continuous improvement tools and methodologies is their interconnection. To detect mistakes that are hindering a process, you first need to identify the root cause of possible issues or threats using a root cause analysis tool. To prevent error from happening you can map the steps of a process through value stream mapping.
9. SIPOC diagram
What is it: The SIPOC (suppliers, input, process, outputs, customers) diagram is a visualizing tool used in the DMAIC methodology (a continuous improvement cycle we presented in our article on Continuous Improvement Processes) to highlight the main stages of the process. It helps establish a common understanding and unify people around the project or problem at stake.
In short, the SIPOC diagram is used to define the inputs and outputs of the process with the goal of determining results and identifying inefficiencies along the way.
Tips for implementation: SIPOC can be as simple as a table where you write down the five elements of the diagram. The suppliers involved in the process, the inputs – the most important resources required, the process that will connect the inputs to the outputs and the steps involved, the outputs and the key results of the process, and lastly, the customer who will benefit from the outputs.
Before creating a SIPOC diagram, write down some key elements: the owner of the process, the name, start and end date of the process, as well as known constraints and feedback loops that will define how you will communicate during the process.
While useful to present the big picture, to improve on the existing processes, it’s usually best used along other tools that can help with the problem solving.
Recommended tools: Many organizations are already using a project management software and they can also be used to create these kinds of diagrams. If you don’t have one in place, you can use a template like the one you can find in the Continuous Improvement toolkit.
No matter the tools and methods in place, at the end of the day they are just a means to an end. As we’ve seen in Toyota’s case, continuous improvement can take years to perfect. But even so, by picking a strategic goal and one of the above-mentioned methodologies and tools, you can start noticing measurable positive change within weeks, or even days, if we’re talking about smaller improvements.
But your work doesn’t stop there. If you want to have long-term results, a systematic approach is essential. So, next we’ll go through some best practices to consider for a good adoption of these methodologies and tools.
Key success factors for successful implementation
• Start small
With every long-term approach, you need to take it step by step by starting with something small. You won’t be able to improve everything at once so it’s best to find your focus, an area you want to improve, or address a challenge your team is facing. At the same time, you need to keep in mind the long-term goals and work towards those, even if at first the progress is small.
If you decide to improve productivity by 15% in the following 6 months, that’s a high bet. You need to first identify the specific areas that slow down productivity and tackle one element at a time.
• Don’t overcomplicate things
In many cases problems are simpler than they seem, and that’s why it’s important to peel their layers and get down to the root cause. The revealed cause might have an easy fix in the end. So, you can’t just guess, you must go beyond assumptions and biases.
Also, if you’re expecting people to include new tools or methodologies in their daily routine you shouldn’t come up with complex terminologies, schemas, or diagrams. For employees from all levels of the organizations to be on board, any new practice should be straightforward and easy to understand. You can work on their complexity gradually, once people start getting used with the basics.
• Accountability is key
To achieve continuous improvement at all levels, you need managers with the right mindset and dedication, who are able to put in the effort to first change their own habits and routines through constant, deliberate practice every day.
But that’s not enough. If you want employees to buy in the continuous improvement approach, they also have to take more responsibility for the company’s success. Continuous improvement won’t succeed unless every team member is on board and engaged in the process.
Manufacturer Roll Forming Corporation identified accountability as the element missing from their continuous improvement program to be successful. So, they came up with a new program to increase accountability through a gainsharing plan which enabled employees to earn more based on their involvement and the improvements visible in their areas.
While this worked for Roll Forming Corporation as a motivator boost that led more people to be accountable, it doesn’t work in all circumstances. Not all companies can afford that and also, it can lead to a culture of mercenaries which can also results in a toxic organizational culture.
When people take responsibility and ownership both for their own success and the company’s they will be more open in adopting new tools and working methods.
• Persistence and resilience
Getting people on board, whether to use new tools, or practice new routines is a constant struggle. But practicing every day for 15 minutes brings more results than practicing two hours once a week.
So, make sure employees are sticking to the improvement routines, and that leaders provide not just a vision and a connecting challenge, but also the time, resources and training that enable them to persist and be resilient.
Conclusion
The famous saying “a man is only as good as his tools” can be true to a certain extent. These tools and methodologies won’t automatically turn your organization into a continuous improvement machine, but they can help you get there. As long as you keep your eyes on the prize and focus on your most important goals, things will start moving in the right direction.
It's also important to remember that there is no one-size-fits-all solution when it comes to tools and methodologies. But with the right mix adapted to your needs, you will start seeing tangible value.
The right tools have the power to address the way you bring about change, and therefore they have a direct influence in how you manage and maintain continuous improvement practices.
Using a digital continuous improvement tool, such as Viima, for running and managing all your continuous improvement processes has many benefits. Book a demo to see it in action!